一、定义与核心特征
1.1基本定义
绕管式换热器是一种专为高压、深冷及强腐蚀工况设计的高效换热设备,以螺旋几何暴力解构传热边界,在深冷高压领域实现 效率、紧凑性、可靠性三重突破,成为现代能源装备的传热核心。冷热流体在管内、管间逆向流动,实现超紧凑传热,适用于LNG液化、空分、氢能等严苛场景。
1.2技术优势
高压耐受性:螺旋缠绕产生的预应力可抵消管内外压差,最高承压达30MPa。
深冷适应性:管束采用低温钢或铝合金,-196℃下仍保持韧性。
自清洁能力:螺旋流道抑制结垢,维护周期延长2~3倍。
热补偿性能:管束自由端可轴向伸缩,避免温差应力集中。
二、结构解析与传热机理
2.1典型结构分解
芯筒:碳钢或不锈钢圆筒,作为管束缠绕基准,直径200~800mm。
螺旋管束:多组细管按15°~30°螺旋角分层缠绕,层间填充定距条。
壳体:高压厚壁筒体,与管束间形成壳程流道,内壁可设导流筒。
管箱:集流管采用多孔锻件,实现管程介质均布。
支撑结构:端部管板与环形支撑圈固定管束,防止振动疲劳。
2.2流体动力学特性
壳程流态:螺旋流道诱导流体旋转,增强湍流度,传热系数提升20%~40%。
管程流态:小管径实现高流速,抑制层流底层热阻。
2.3传热强化机制
逆流主导:管程与壳程逆向流动,对数平均温差大化。
二次流效应:螺旋曲率诱发Dean涡流,强化边界层扰动。
高密度传热面:通过多层缠绕与密排管束,单位体积传热面积达管壳式3倍以上。
三、绕管式换热器制造工艺与质量控制
3.1核心制造流程
管束预成型:
细管经矫直、酸洗后,在芯筒上螺旋缠绕,层间铺设铜制定距条。
缠绕张力控制,确保管束层间紧密贴合。
管束固定:
端部采用环形锻件+电子束焊接,形成整体管束模块。
液压胀管使管束与芯筒贴合。
壳体组装:
厚壁筒体卷制+纵缝焊接,内壁堆焊耐蚀层。
管束整体吊装入壳,两端法兰螺栓预紧。
3.2特殊工艺要求
深冷处理:管束在液氮中冷却至-196℃,释放缠绕残余应力。
氦检漏测试:管程充氦至设计压力,质谱仪检测泄漏率<1×10⁻⁹mbar·L/s。
流阻测试:壳程水循环测试,压降偏差≤5%。
3.3数字化制造技术
缠绕数控系统:6轴机器人同步控制管材送进与芯筒旋转,定位精度±0.1mm。
AI工艺优化:基于历史数据训练神经网络,预测理想缠绕张力与速度组合。
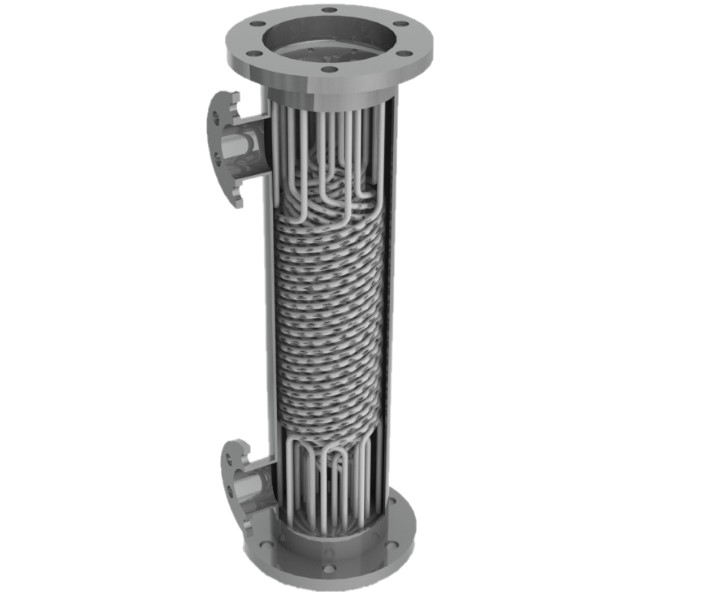